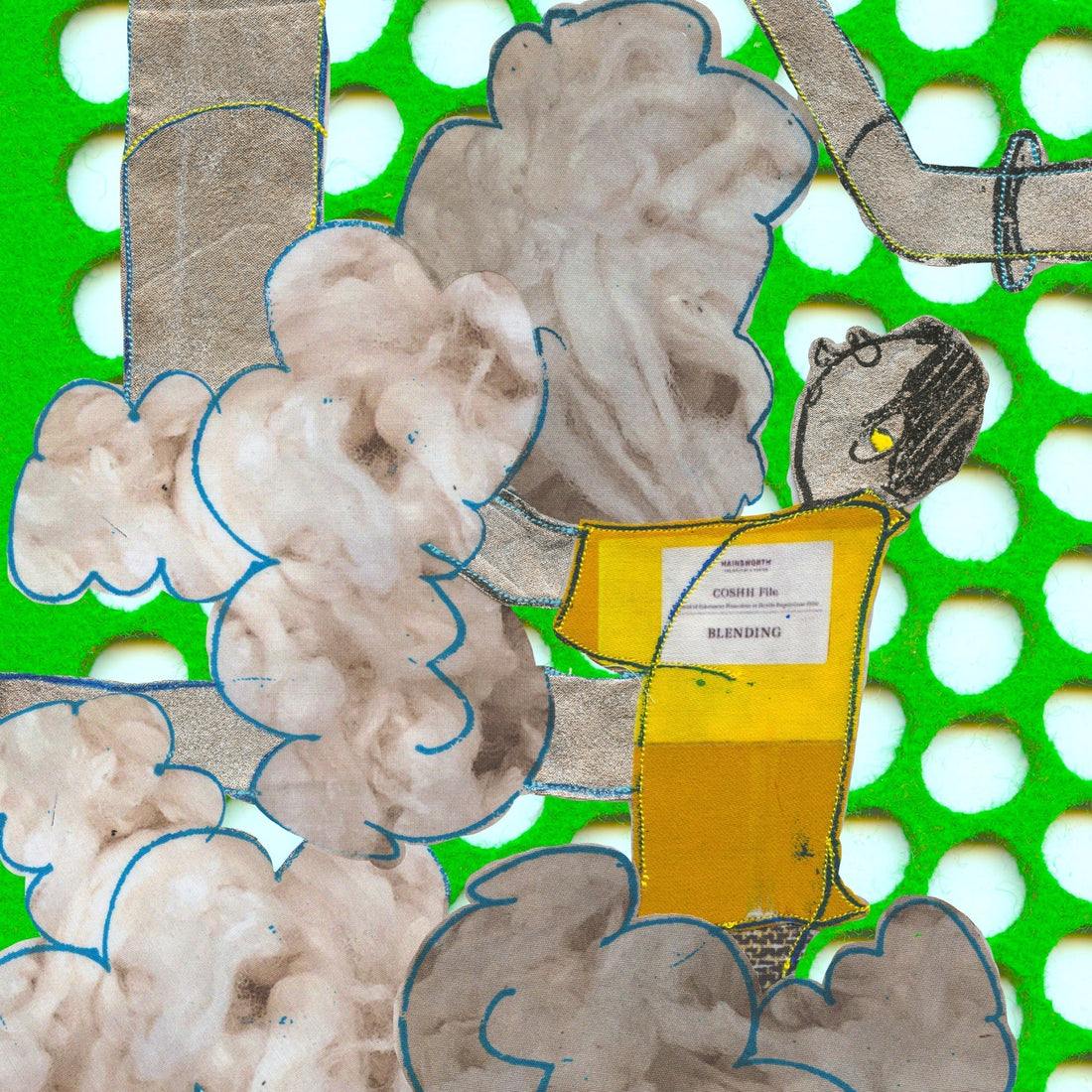
Run of the Mill: AW Hainsworth
What do firefighters, Buckingham Palace guards, and Steinway pianos all have in common? They are all adorned with cloth produced and woven by AW Hainsworth, a family-run West Yorkshire mill. Although the name may be unfamiliar, readers will most certainly have seen—or perhaps even worn—Hainsworth fabrics.
The scarlet tunics of the Royal Guards are instantly recognised around the world. UK firefighters put their lives in the hands of the fire-retardant uniforms created by the weavers in Spring Valley Mills, and customers around the globe rejoice in wearing the finest garments created by designers and fashion houses such as Prada and Valentino, which have sourced their fabrics from AW Hainsworth.
The mill was founded by Abimelech Hainsworth (at the age of 14) in 1783, but it is now run by 7th-generation Tom Hainsworth, whose eyes are very much focused on the present and the future. Employing around 200 people in the Stanningley mill itself and a further 15 in the dye house, AW Hainsworth is invested in developing the next generation of textile experts.
Picking and Mending. Rachael Howard.
“Our current workforce is full of knowledge and expertise, and we want to make sure these skills are passed on to the next generation,” says Charlotte Law from AW Hainsworth. “This is not just so we can protect the mill’s future but also the future of the UK textiles industry. Textile manufacturing is a highly specific craft, developed over centuries, and it’s one that we’re proud to help flourish in the UK.”
This centuries-old craft involves many meticulous stages that are crucial for the wool fibres to be carefully nurtured into the beautiful cloth used for fashion, PPE, interiors, snooker tables, and even woven wool felt that provides cushioning within pianos. Having all of these stages crafted, checked, and delivered under one roof allows the company to respond to supplier and customer needs while researching innovative techniques—carefully tested by the team of in-house fabric technologists—and maintaining a competitive edge.
Woolstore Blue, Rachael Howard.
The story of this unique vertical mill begins in the Wool Store, where the finest lamb’s wool, merino and cashmere, handpicked from sheep farms across Britain, Australia, and New Zealand, is gathered. Climate impacts the wool quality, and each fibre is selected for its blending potential.
Fibres are then blended, which is where science meets creativity. Raw wool is combined to create fibre mixes for individual products. Fibres are gently teased apart by opening machines that remove impurities, while fine lubricant is added to ensure fibres remain damage-free. The wool is then layered, mixed, and pneumatically moved into a fearnought picker for final refinement.
Carding. Rachael Howard.
The wool then goes through carding, which is the disentangling and cleaning process that results in a continuous web or sliver. This web works through “swifts,” “workers,” and “strippers” – a series of rollers—that align the fibre web into narrow strips. These strips are then formed into clubbings that are wound onto condenser bobbins ready for spinning.
Spinning breathes life into the fibres, turning slubbings into yarn. This process is all about precision – drafting machines stretch the fibres while spindles spin them into yarns with customised thickness and twist. The interplay of speed and tension gives the yarn its unique character, setting the foundation for the fabric’s strength and finesse, ready for warping.
Warping. Pressing Machine Button. Rachael Howard.
Warping sets the stage for weaving. Cones of yarn are placed onto a creel, where they are aligned in parallel lengths under equal tension and spacing. The yarn winds onto a warping balloon and then a warping beam, ready for the loom.
The weaving process takes place in the weaving shed, where warp and weft threads interlace on the looms. These looms handle everything from fine, delicate fabrics to broad and bold designs. The AW Hainsworth looms can weave fabric widths stretching up to 452 cm.
Dyeing. Rachael Howard.
The process then moves into the dye house, where colour is infused into the fabric with the ultimate goal of achieving a uniform distribution using a winch, jet-dyeing machines, and bespoke techniques. Every shade is meticulously checked against a database to guarantee consistency.
The fabric is then required to be carefully dried (tentering). The phrase “on tenterhooks” refers to this vital stage of textile production when the fabric is drying, which is a crucial stage to ensure the fabric retains its shape and there is no shrinkage, nodding to tradition and modern expertise.
Mending and Picking. Rachael Howard.
And so to the final flourish! The finishing process is where the Hainsworth charm shines through, with a series of specialised processes applied to the woven and set fabrics for the individual effects. Raising machines lift fibres to create bespoke finishes, and the Hainsworth drape, handle face, and sheen emerge. Boiling and blowing machines set fabrics, while padding machines apply finishes, and brushing machines add a final fibre alignment.
The result of this fine-tuned weaving process is a fabric that has stood the test of time and is regarded as innovative in today’s forward-thinking textiles industry. In addition, AW Hainsworth achieves all of this while being environmentally conscious, with various initiatives in place around carbon emissions, saving water, recycling, and a goal to reach Zero Landfill.
“This hasn’t been without its challenges,” Law says, “but we’ve been encouraged by the results we’ve seen so far, and I’m proud of the collective effort our workforce is making. We often say that sustainability isn’t just about grand gestures. It can be achieved through small steps leading to our larger goals. By championing sustainability at all levels of the business, we can continue to reduce our environmental impact year on year.”
She adds: “AW Hainsworth have always been innovators; it is built into our heritage. In the 1860s, we supplied the London Fire Brigade with our wool melton cloth, the most flame-retardant fabric available at the time, and we continue developing technically advanced solutions. We work closely with customers and partners across many industries to develop new solutions, ensuring we listen to our end users. Innovation is part of our identity as a business, which makes finding the balance between our heritage and the future much easier to do.”
In addition to pushing the boundaries, AW Hainsworth has gained an enviable reputation for its empathic approach to its workforce family – with on-site and prioritised mental health support – and its social conscience. The firm partners with local Yorkshire charity Zarach, working to end bed poverty in Leeds. Hainsworth provides financial support throughout the year and donates woollen blankets it manufactures in the mill.
This sounds like a good blend of celebrating history and tradition and a social awareness of how innovative ideas can be woven to create a significant impact across multiple lives and sectors.
Words by Jennifer Harper
Illustrations: Rachael Howard
-
Further Information: